数控磨床如何设置加工原点数控磨床设置加工原点的步骤数控磨床加工步骤
Time:2023-11-25 12:35:10
关于数控磨床如何设置加工原点的问题,我们总结了以下几点,给你解答:
数控磨床如何设置加工原点
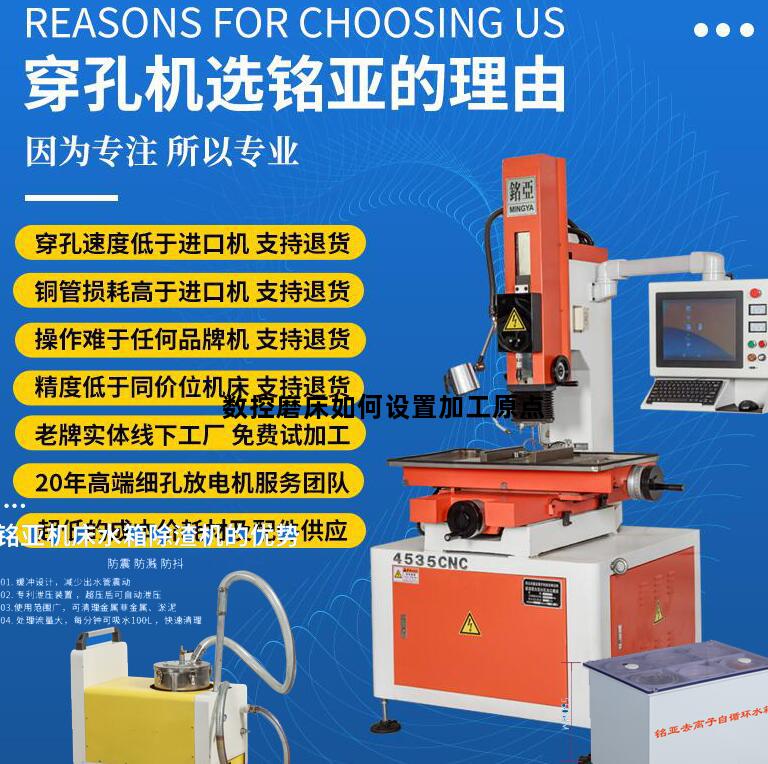
Sg一、工件坐标系的建立方法
1、转动刀架至基准刀(如1号刀), 在MDA状态下,输入T1D0,使刀补为0,机床回参考点。
2、用试切法确定工件坐标原点。先切削试件的端面。Z方向不动。若该点即为Z方向原点,则在参数下的零点偏置于目录的G54中,输入该点的Z向机械坐标值A的负值,即Z=-A。若Z向原点在端面的左边处,则在G54中输入Z=-(A+),回车即可。
同理试切外圆,X方向不动。Z方向退刀,记下X方向的机床坐标A,量直径,得到半径R,在G54的X中输入X=-(A+R),回车即可。
二、设定数控车床的工件坐标系 工件坐标系是编程时使用的坐标系,又称编程坐标系,该坐标系是人为设定的。建立工件坐标系是数控车床加工前的必不可少的一步。不同的系统,其方法基本相同。
扩展资料:
机床坐标系:
1、机床坐标系( Machine Coordinate System )是以机床原点O为坐标系原点并遵循右手笛卡尔直角坐标系建立的由X、Y、Z轴组成的直角坐标系。 机床坐标系是用来确定工件坐标系的基本坐标系。是机床上固有的坐标系,并设有固定的坐标原点。
2、工件坐标系(编程坐标系)工件坐标系是编程时使用的坐标系,所以又称为编程坐标系。数控编程时,应该首先确定工件坐标系和工件原点。零件在设计中有设计基准。在加工工艺基准,同时要尽量将工艺基准与设计基准统一,该基准点通常称为工件原点。
3、工件坐标系设定:执行G(50) X(α ) Z( β)后,系统内部即对(α,β)进行记忆,并显示在显示器上,这就相当于在系统内部建立了一个以工件原点为坐标原点的工件坐标系。
4、同一工件由于工件原点变了,所以程序段中的坐标尺寸也随之改变。因此,在编制加工程序前必须首先确定工件坐标系(编程坐标系)和工件原点(编程原点)。
参考资料来源:百度百科--机床坐标系
一、机器坐标系的建立方法:
首先,将机床工作台移动到预设的原点位置,然后将机床控制器进入手动模式,通过手动操作使工作台移动到三个坐标方向(X、Y、Z)的正方向终点,记录下此时的三个位置坐标值,分别为X0、Y0、Z0。再通过控制器程序输入指令,将机床坐标原点 (X0、Y0、Z0) 设置为机床坐标系原点。
二、工件坐标系的建立方法:
工件坐标系是基于工件进行设置的坐标系。首先将工件放置在机床工作台上,然后将机床工作台移动到工件上要加工的特定位置(即零件的原点),通过控制器程序输入指令,将机床坐标原点 (X0、Y0、Z0)设置为工件坐标系的原点,然后通过控制器程序增加偏差量,将工件坐标系与机器坐标系建立关联,从而使得机床控制器产生相应的运动轨迹,实现对工件的加工和加工质量的控制。
数控车床前对刀原理及对刀方法
注意:运行程序前要先将基准刀移到设定的位置。
在用G50设置刀具的起点时,一般要将该刀的刀偏值设为零。
此方式的缺点是起刀点位置要在加工程序中设置,且操作较为复杂。但它提供了用手工精确调整起刀点的操作方式,有的人对此比较喜欢。
(3)用G54~G59设置程序原点
①试切和测量步骤同前述一样。
②按“OFSET SET”键,进人“坐标系”设置,移动光标到相应位置,输入程序原点的坐标值,按“测量”或“输入”键进行设置。如图4所示。
③在加工程序里调用,例如:G55 X100 Z5...。G54为默认调用。
注意:若设置和使用了刀偏补偿,最好将G54~G59的各个参数设为0,以免重复出错。对于多刀加工,可将基准刀的偏移值设置在G54~G59的其中之一,将基准刀的刀偏补偿设为零,而将其它刀的刀偏补偿设为其相对于基准刀的偏移量。
这种方式适用于批量生产且工件在卡盘上有固定装夹位置的加工。铣削加工用得较多。
执行G54~G59指令相当于将机床原点移到程序原点。
(4)用“工件移”设置程序原点
①通过试切工件外圆、端面,测量直径,根据公式(1)计算出程序原点(工件原点)的X坐标,记录显示屏显示的原点Z坐标。
②按“OFSET SET”键,进入“工件移”设置,将光标移到对应位置,分别输入得到的X. Z坐标值,按机床MDI键盘上的“INPUT”键进行设置。如图5所示。
③使X、Z轴回机床原点(参考点),建立程序原点坐标。
“工件移”设置亦相当于将机床原点移到程序原点(工件原点)。对于单刀加工,如果设置了“工件移”,最好将其刀偏补偿设为0,以防重复出错;对于多刀加工,“工件移”中的数值为基准刀的偏移值,将其它刀具相对于基准刀的偏移值设置在相应的刀偏补偿中。4 多刀对刀
FANUC数控系统多刀对刀的组合设置方式有:①绝对对刀;②基准刀G50+相对刀偏;③基准刀“工件移”+相对刀偏;④基准刀G54~G59+相对刀偏。
(1)绝对对刀所谓绝对对刀即是用每把刀在加工余量范围内进行试切对刀,将得到的偏移值设置在相应刀号的偏置补偿中。这种方式思路清晰,操作简单,各个偏移值不互相关联,因而调整起来也相对简单,所以在实际加工中得到广泛应用。
(2)相对对刀所谓相对对刀即是选定一把基准刀,用基准刀进行试切对刀,将基准刀的偏移用G50,“工件移”或G54~G59来设置,将基准刀的刀偏补偿设为零,而将其它刀具相对于基准刀的偏移值设置在各自的刀偏补偿中。
下面以图2所示为例,介绍如何获得其它刀相对基准刀的刀偏值。
①当用基准刀试切完外圆,沿Z轴退到a点时,按显示器下方的“相对”软键,使显示屏显示机床运动的相对坐标。
②选择“MDI”方式,按"SHIFT"换档键,按"XU"选择U,这时U坐标在闪烁,按“ORIGIN”置零,如图6所示。同样将w坐标置零。
③换其它刀,将刀尖对准a点,显示屏上的U坐标、W坐标即为该刀相对于基准刀的刀偏值。此外,还可用对刃仪测定相对刀偏值。5 精确对刀
从理论上说,上述通过试切、测量、计算;得到的对刀数据应是准确的,但实际上由于机床的定位精度、重复精度、操作方式等多种因素的影响,使得手动试切对刀的对刃精度是有限的,因此还须精确对刀。
所谓精确对刀,就是在零件加工余量范围内设计简单的自动试切程序,通过“自动试切→测量→误差补偿”的思路,反复修调偏移量、或基准刀的程序起点位置和非基准刀的力偏置,使程序加工指令值与实际测量值的误差达到精度要求。由于保证基准刀程序起点处于精确位置是得到准确的非基准刀刀偏置的前提,因此一般修正了前者后再修正后者。
精确对刀偏移量的修正公式为:
记:δ=理论值(程序指令值)-实际值(测量值),则
xo2=xo1 +δx(3)
Zo2=Zo1-δZ
注意:δ值有正负号。
例如:用指令试切一直径40、长度为50的圆柱,如果测得的直径和长度分别为040.25和49.85,则该刀具在X、Z向的偏移坐标分别要加上-0.25和-0.15,当然也可以保持原刀偏值不变,而将误差加到磨损栏。6 结束语
笔者设计了一段多刀加工程序,在FANUC Oi数控车削系统上验证了上述几种组合对刀设置方式,取得了相同的效果。对其它数控系统也具有一定推广价值。
参考资料:http://ati.nstl.gov.cn/car/tech/150201_2.asp
出现故障的原因可能是限位器出问题了(进水短路)
事先应该查看说明书 将机械回零的电限位开关参数关掉 或者直接把他拆了(要不然会出问题奥)
手动 或者 单步 将各轴移动至最大位置(你的机械坐标零点) 在手动或者单步状态下按住 '取消"键再按x x轴当前位置既设定为机械零点 z轴步骤相同
安装这样的轴承是高级钳工干的活 一般人弄不了...
数控磨床加工步骤
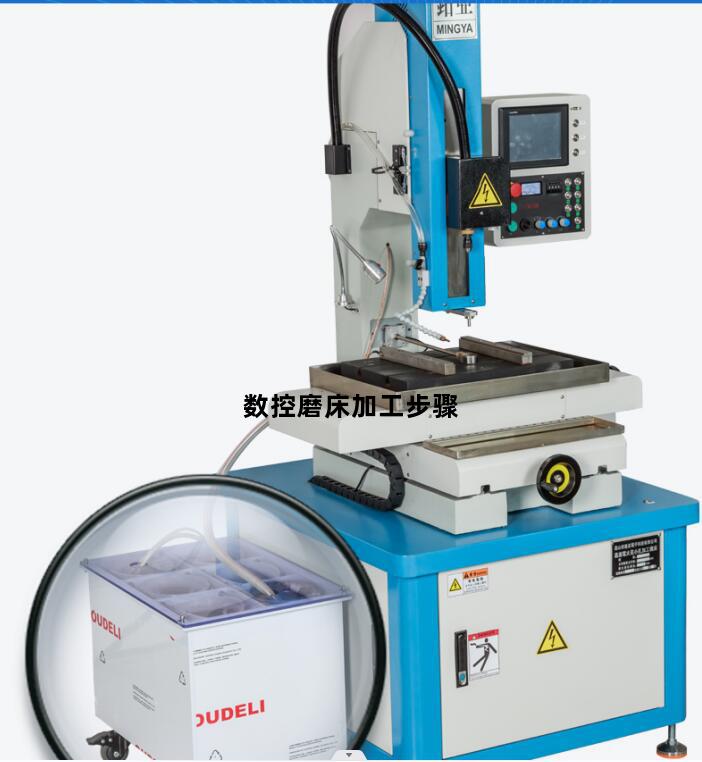
修整砂轮,,,,, 加工磨外圆,,,
············································
数控磨床设置加工原点的步骤
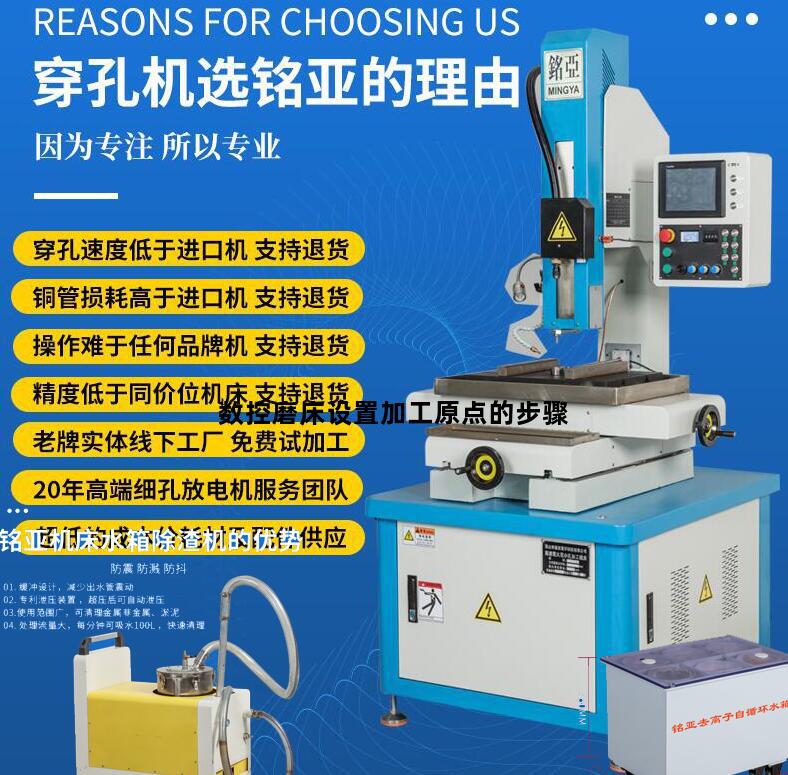
本文拓展问题:
数控磨床指令,
数控磨床怎么对刀,
数控磨床如何设置加工原点。